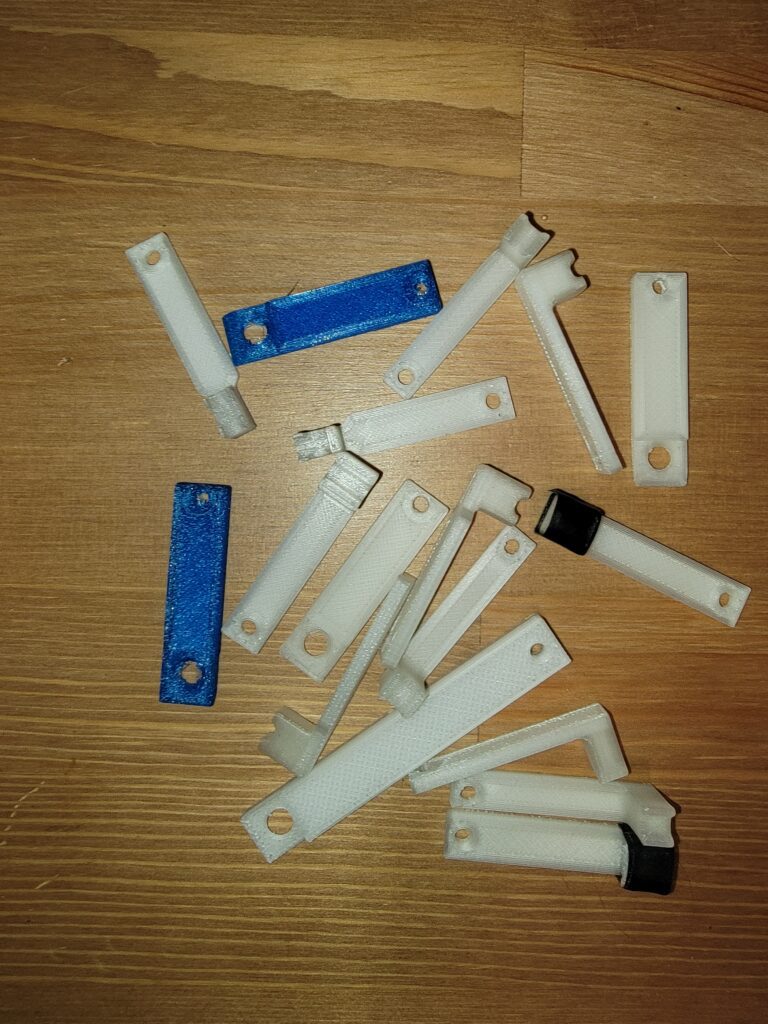
In many automated assembly applications, a well-thought-out custom gripper design is essential. In this article I’ll talk about the process and iterations needed to accomplish the Meca 500 Diode Load sequence in RoboFiesta’s Mecademic Meca 500 Diode Loading Demo on YouTube.
Some of the things you’ll need to consider are:
- What’s being gripped / picked. Dimensions, fragility, prestage setup
- Speed required for the application
- Precision / repeatability required for the application
- Incoming material variability
- Placement location with regards to EOAT orientation
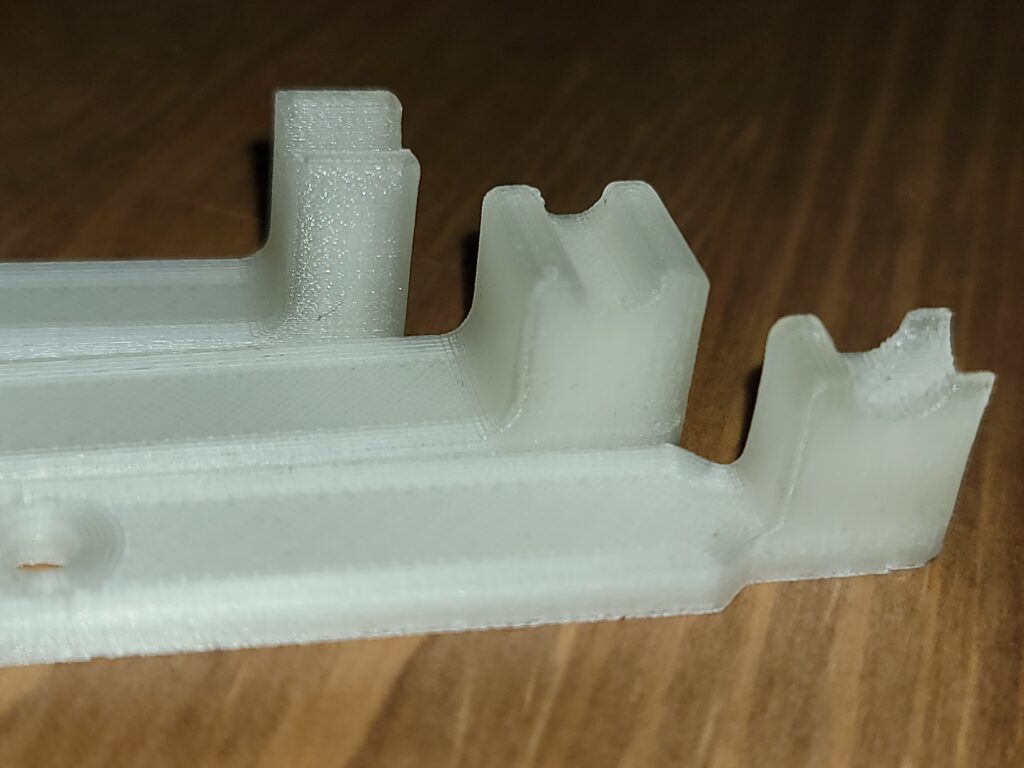
For a part in a given location / orientation- a diode mounted on a breadboard, for instance- the gripper design would need to change depending on which direction the gripper fingers extend from the gripper mechanism.
It’s a good idea to do some dry runs with mock material to determine the requirements. For the diode handling, we could have picked with the gripper fingers extending in either X or Z from the mechanical gripper body mounted on the robot flange:
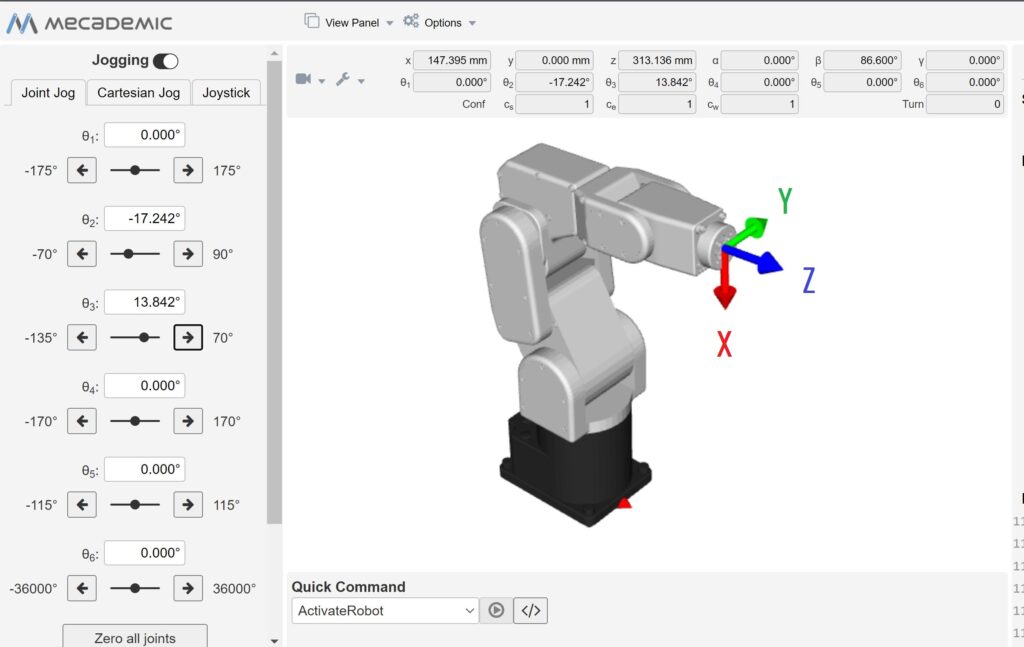
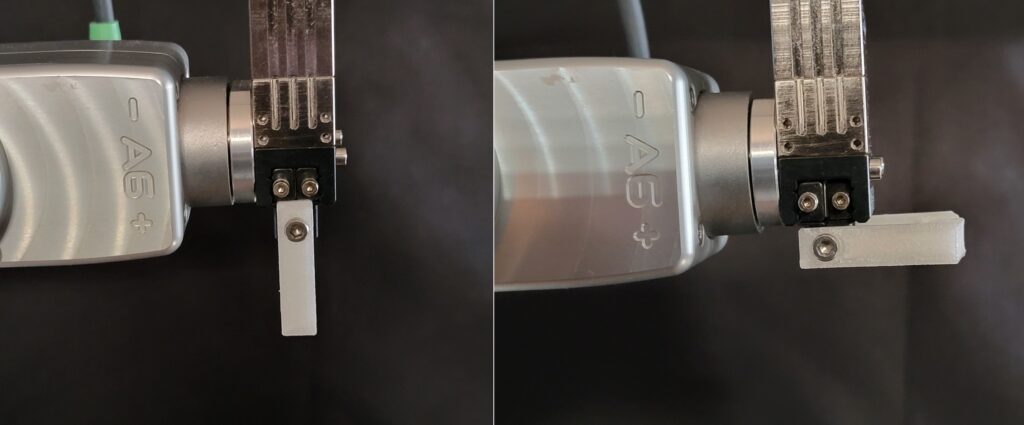
Which directions the gripper fingers extend also affects the toolpath you will program. In our diode sequence, the gripper fingers extend down in X from gripper body.
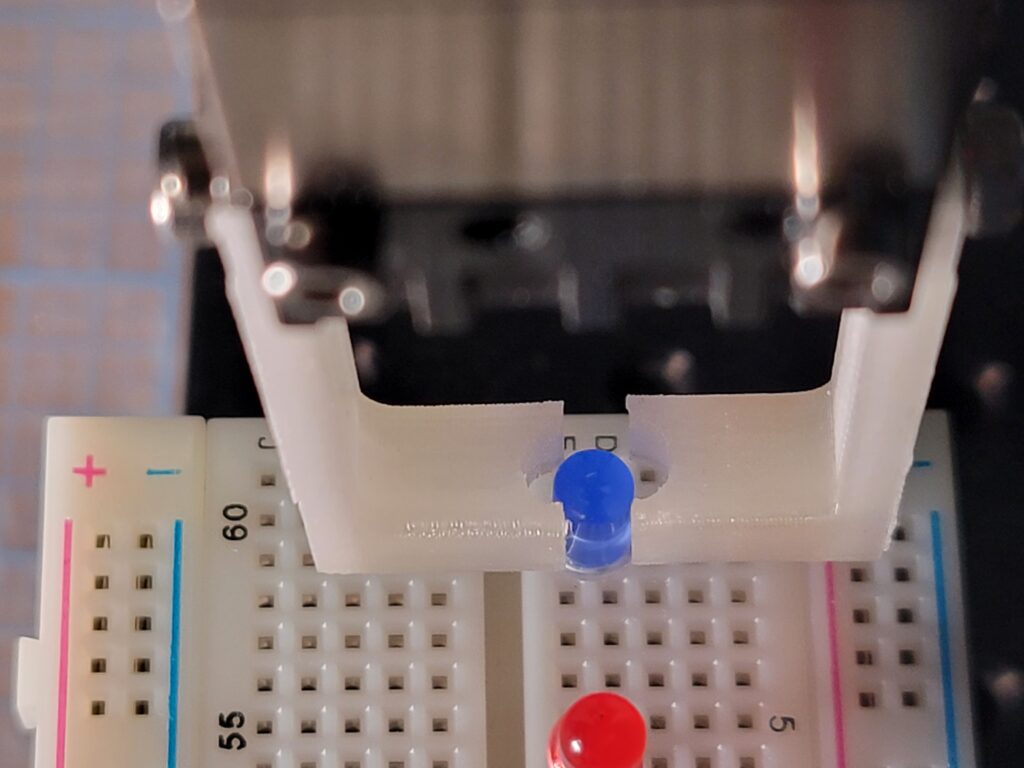
It took several iterations of grippers to develop a design that would firmly grasp the slightly tapered diode body without slipping. The final design featured a small relief or notch feature to accommodate a small lip on the bottom of the diode body.
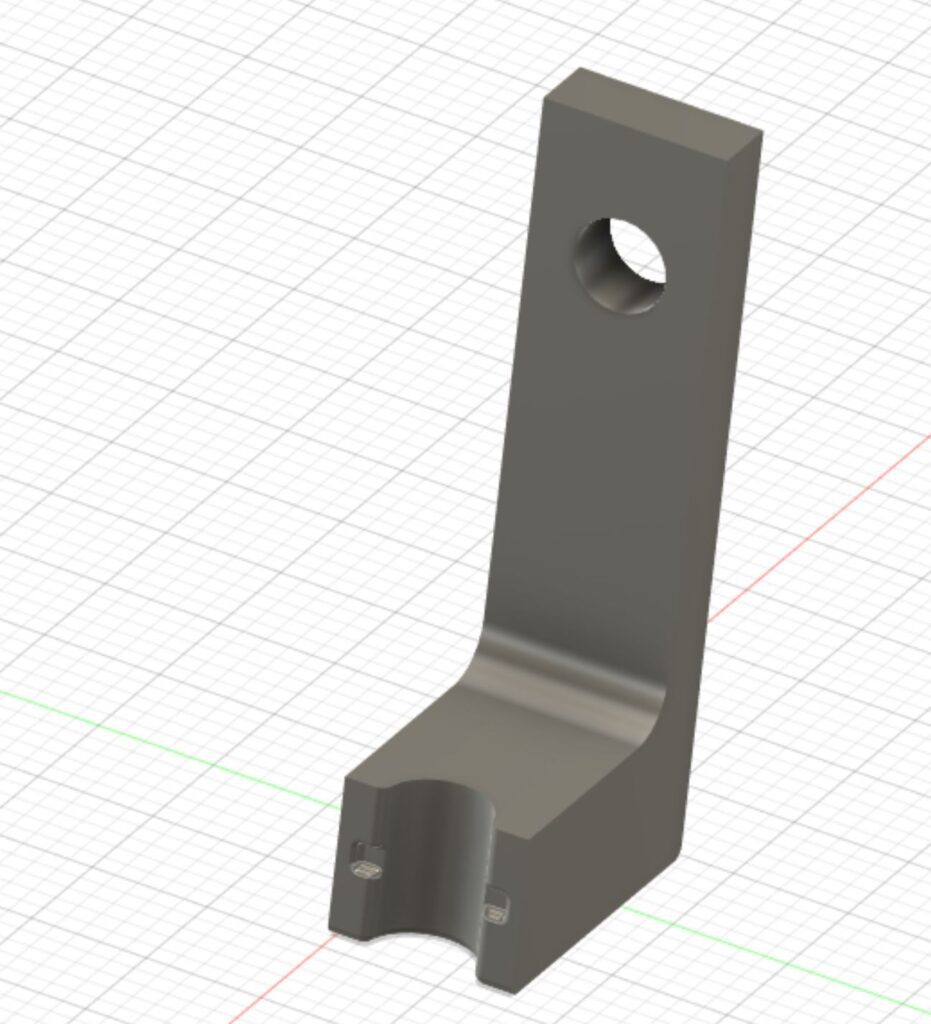
Finally, having a capable 3D printer like the Flashforge Creator Pro is invaluable for on-the-fly iterations for functionality and changes in setup orientation of your grippers. I’m currently using 1.75mm ABS Transparent filament, it’s a great material for general purpose applications.
Watch a timelapse of a gripper print here.
There are other factors to take into consideration depending on the situation, but those are the basics I start with when making new gripper designs.
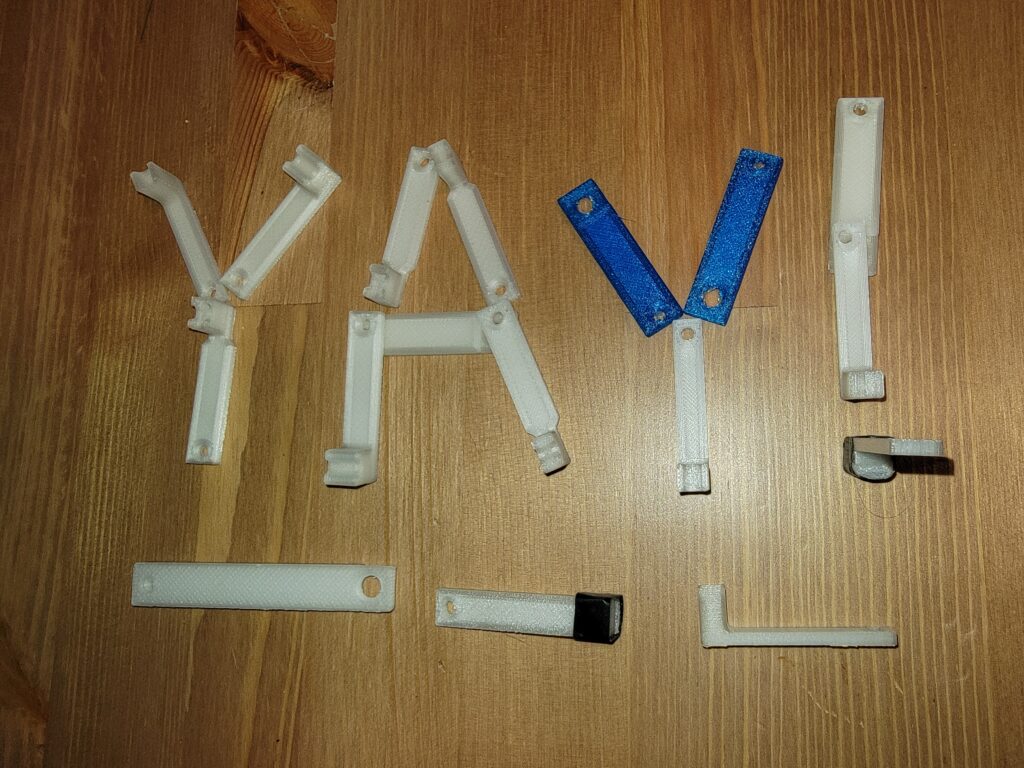